Upgrading rail infrastructure—whether it’s access platforms, staircases, or handrails—requires careful consideration of safety and long-term costs. One of the most critical safety factors is how materials react to electrical currents. In the rail industry, earthing and bonding are necessary when using traditional materials like steel, adding both complexity and cost to any project. Fibreglass Reinforced Plastic (FRP), however, is non-conductive, making it an ideal choice for rail projects that prioritise safety and cost-efficiency.
What is Earthing?
Earthing is a process where electrical systems are connected to the ground. This ensures that in the event of a fault—such as an electrical surge or malfunction—electricity is directed safely into the earth. In rail settings, where high-voltage equipment is common, earthing is critical to protect both workers and passengers from electric shocks or fires.
What is Bonding?
Bonding involves connecting all conductive parts of a structure or system together so that any differences in electrical potential are neutralised. This process prevents stray voltage from causing electric shocks when multiple pieces of metal (like handrails, platforms, or other structures) are in close proximity to electrical systems.
Hidden Costs of Earthing and Bonding with Steel
In a rail environment, earthing and bonding are essential for ensuring the safety of both the public and workers. Without proper earthing, an electrical fault could result in deadly consequences—such as electric shocks or fires—when someone touches a conductive surface like a metal handrail or platform.
This is particularly important in areas where rail infrastructure is near high-voltage equipment, such as overhead power lines or electrified rail tracks. Any structure made from steel or aluminium requires extensive earthing and bonding – this process must be done meticulously to meet required safety regulations, which makes these projects not only more expensive but also more time-consuming. The larger and more complex the structure, the higher the cost.
Steel structures, in particular, require these additional safety measures due to their highly conductive nature. Every piece of exposed steel must be bonded and earthed, and any mistakes in installation can have severe consequences—not just for safety, but for ongoing maintenance costs and regulatory compliance.
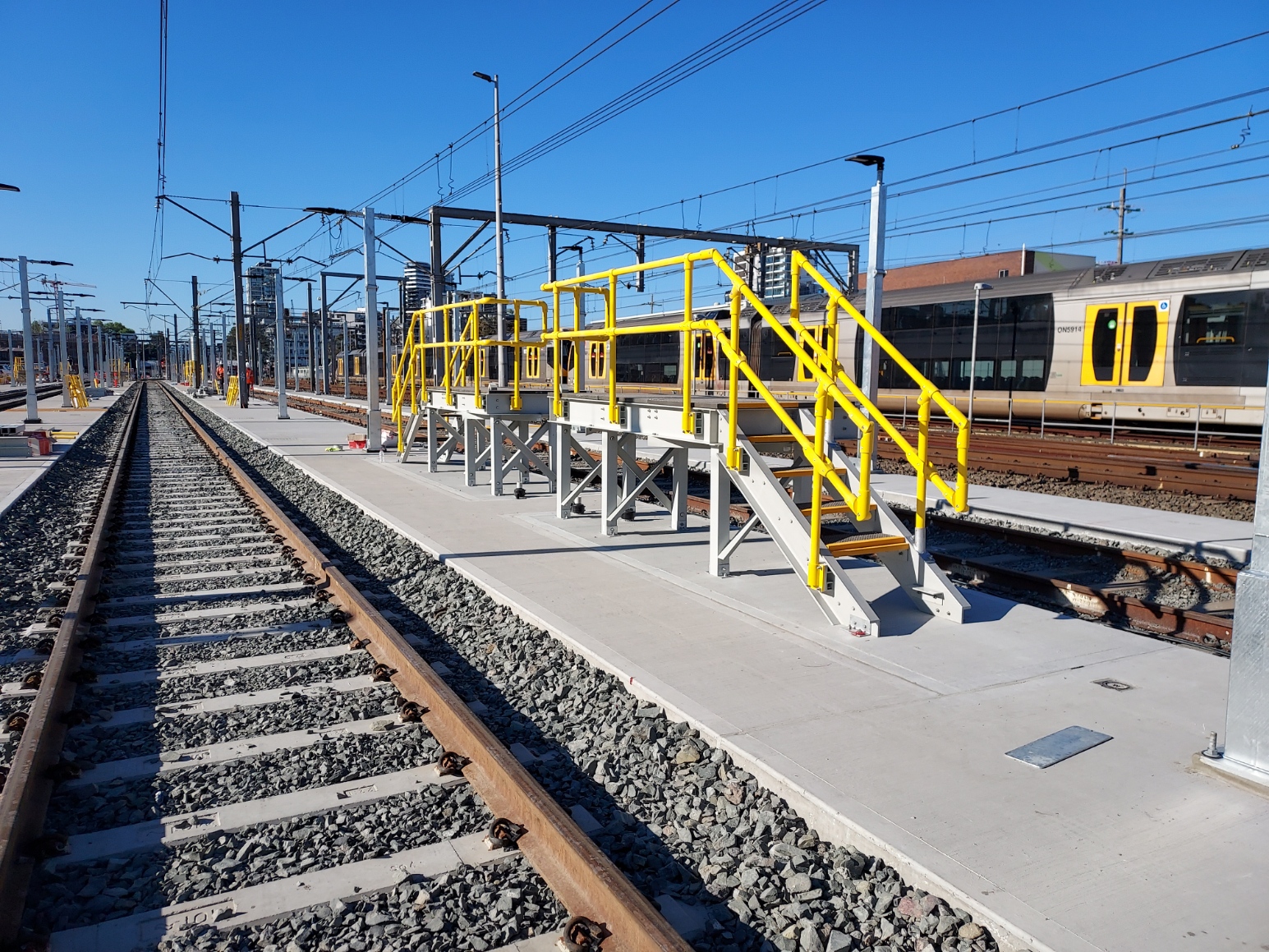
Eliminating Earthing and Bonding with Fibreglass Reinforced Plastic (FRP)
This is where Fibreglass Reinforced Plastic (FRP) provides added value and helps with minimizing additional costs in your rail upgrades and development. FRP is non-conductive, meaning it doesn’t carry electrical currents the way steel or aluminium does. As a result, there’s no need for earthing and bonding when using FRP in rail infrastructure.
By removing this requirement, FRP significantly reduces installation costs and streamlines project timelines. There’s no need to invest in specialised labour, additional materials, or complex systems to ensure safety. The non-conductive nature of FRP also reduces the risk of electrical hazards, providing a safer environment for both workers and passengers.
By choosing FRP developers can cut installation costs, reduce ongoing maintenance, and ensure a safer, more efficient infrastructure upgrade—all while meeting the stringent safety standards required in the industry.